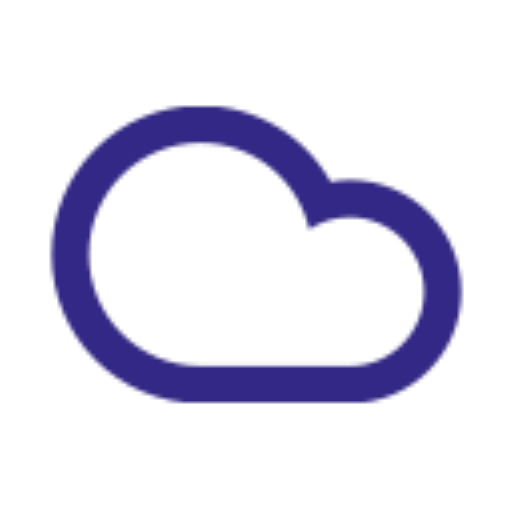
This
comprehensive welding course covers various welding techniques and positions,
including 1G, 2G, 3G, 4G, 6G, 6G ARC, 6G T.I.G, as well as welding on specific
materials such as carbon steel, stainless steel, copper-nickel, duplex, super
duplex, and M.I.G & MAG. The course duration is three months, and it offers
a total of 78 job opportunities upon completion.
This welding course
caters to individuals who have a keen interest in pursuing a career in welding,
as well as those who are already employed in the field. It is well-suited for
aspiring welders, welding technicians, and professionals who aim to refine
their welding skills and specialize in specific techniques and materials. By
successfully completing this course, participants can establish a rewarding
career both within their own country and internationally, with the potential
for significant income opportunities.
While no specific prerequisites are mentioned, basic knowledge of welding concepts and techniques is recommended. Familiarity with welding safety practices, equipment, and tools will be advantageous. Some courses may require prior experience or certifications in welding.
Upon completing
this welding course, participants can expect to acquire the following skills:
Proficiency in Different
Welding Positions: Participants will develop expertise in various welding
positions, such as 1G, 2G, 3G, 4G, 6G, 6G ARC, and 6G T.I.G. They will learn
the techniques and challenges associated with each position.
Specialized Welding on Specific
Materials: The course will focus on welding techniques for specific materials,
including carbon steel, stainless steel, copper-nickel, duplex, super duplex,
and more. Participants will learn how to weld these materials effectively and
produce high-quality welds.
Advanced Welding Techniques:
Participants will gain hands-on experience in advanced welding techniques like
M.I.G (Metal Inert Gas) and MAG (Metal Active Gas) welding. They will learn how
to use these techniques to join metals efficiently and accurately.
Weld Quality and Inspection:
Participants will develop skills in assessing weld quality and performing
visual inspections. They will learn to identify common weld defects, understand
their causes, and implement corrective measures to ensure weld integrity.
Stick
welding, also known as Arc welding, is a traditional and relatively affordable
method. It involves using a stick electrode welding rod to create an electric
arc that melts the metal and forms a weld. Stick welding is commonly used in
construction, maintenance, and repair work.
MIG (Metal Inert Gas) welding
is a popular choice for beginners and DIY enthusiasts. It utilizes a wire
electrode that is continuously fed through a welding gun. MIG welding can join
thin metal pieces and is versatile for various materials. It can be done with
or without a shielding gas, using flux core wire.
TIG (Tungsten Inert Gas)
welding is a precise and versatile technique that produces high-quality welds.
It requires two hands, one for feeding the filler rod and the other for
operating the TIG torch. TIG welding is commonly used for welding thin sections
of stainless steel, aluminum, and other metals in industries such as
automotive, aerospace, and art fabrication.
Plasma
arc welding is a precise method used in aerospace and other industries where
precision and thin materials are involved. Similar to TIG welding, it utilizes
a tungsten electrode, but the electrode is recessed and ionizing gases are used
to create the heat. Plasma arc welding is suitable for welding materials as
thin as 0.015 of an inch.
Electron beam and laser welding
are high-energy techniques that offer exceptional precision and power. They are
commonly used in industries such as medical device manufacturing and aerospace.
These processes provide the ability to weld small, intricate parts with great
accuracy and can also handle larger components. They offer both metallurgical
and aesthetic advantages and can be cost-effective.
Gas welding, which uses a
mixture of oxygen and acetylene, is a portable method that was once popular but
has been largely replaced by other techniques like TIG welding. It is still
occasionally used for specific applications such as welding car exhaust
components.
Hhs
Shhs
Report as Inappropriate